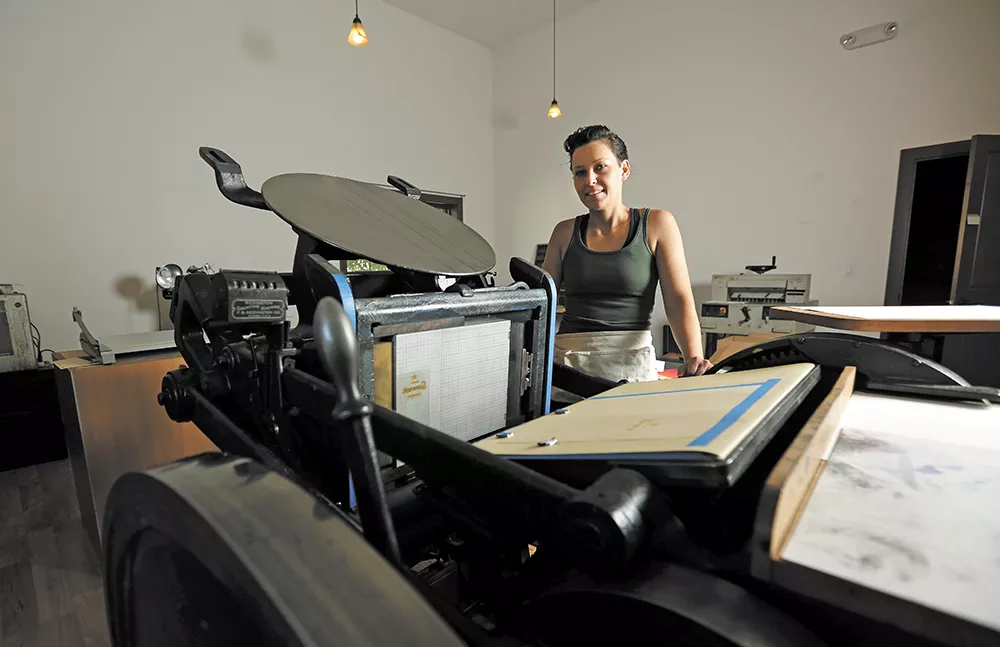
Breanna White needed to work with her hands — anything more tangible than spending hours upon hours in front of a computer, anchored to the mouse and keyboard.
One day she glanced an advertisement seeking a letterpress print shop intern. Without even knowing what a letterpress was, she decided to inquire.
"The first time I made an impression, it was like, 'This is what I want to do,'" White recalls of that first time operating a press. At that time, she was working toward her degree in visual communication and graphic design from the Illinois Institute of Art in Chicago.
Five years later, and White is now operating her own one-woman shop and design studio, Typebee Letterpress Printshop, out of a cozy Post Falls warehouse.
The scent of ink, paper and plate-washing solvents lingers in the air. Illuminated by the mid-morning sunlight coming through an open window is her main machine, a finicky and noisy 1926 Chandler & Price printing press. Grabbing an orange extension cord from the corner of the room, White fires up the hulking, cast-iron beast. Its electric motor hums as the gears crank to life, moving the press's metal parts into a rhythmic clank-and-clatter song and dance.
It all started here for Typebee about two years ago when White offered to help restore the 90-year-old printing press, purchased by DOMA Coffee Roasting Co., to print its coffee bags featuring local artists' designs. As Typebee, White still prints labels and other marketing materials for the sustainability-focused, local roaster.
To many, the concept of letterpressing may bring to mind the tedious process of hand-setting individual letters (called "sorts") into lines of mirror-reversed type. White doesn't hand-set her own type. Rather, she creates or manipulates images and text digitally, sending off the files to one of two companies in New York that manufacture printing plates. Depending on the job, she'll have plates made from either magnesium or polymer.
"I don't think letterpress would exist still today without digital technology," she remarks.
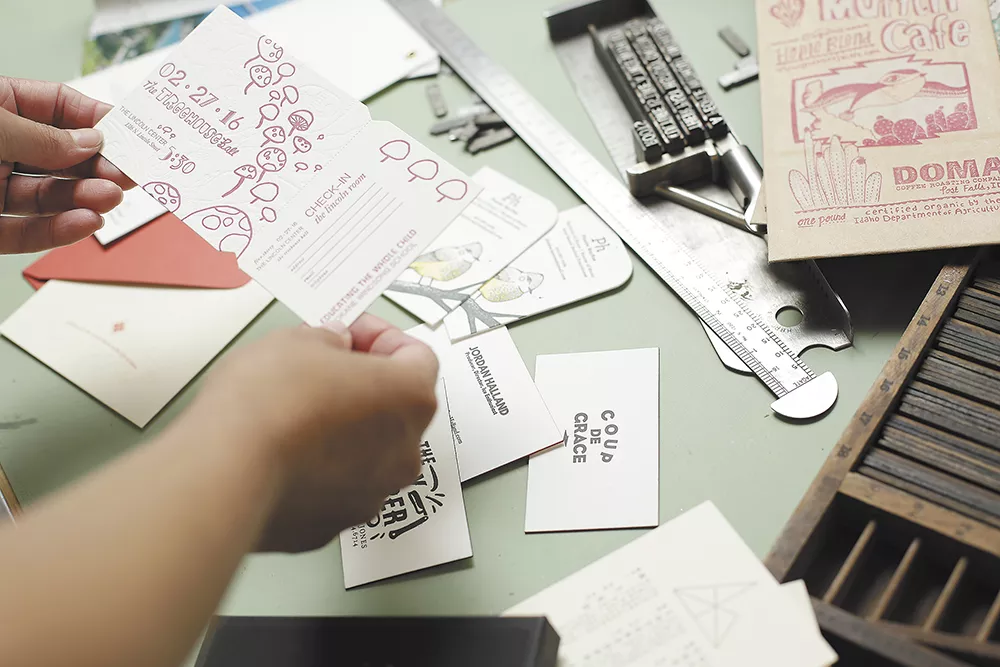
Without digital tools, making plates of, say, a custom illustration by a local artist would require someone with the skills to carve an image into a printable surface. The melding of digital techniques with the manual craft of letterpress printing allows White to work more efficiently, even if her overall method is many steps back from the digitized and automated nature of today's printing industry.
"Typesetting is more for fun these days, and there are still people who do that — it's not cost effective or efficient, but this is neat because it's where technology and old-world craftsmanship come together nicely," she says.
Another major difference between modern letterpressing versus the craft of yesteryear is that now printers are often looking to achieve a debossing effect in which the typeface or outline of an inked image makes a visible impression into the paper. This textured effect was considered bad technique by letterpress operators in the past — their goal was to smoothly ink a page leaving no visible indentation on the paper.
"I think people gravitate toward letterpress because they can touch it and it gives them something to feel. You can't create that on a computer," White muses.
The range of work White can create by letterpress spans from business cards, wedding and event invitations, postcards and beyond; she's pressed cassette tape inserts for a French band, custom stationary and drink coasters. The presses can also be used to score and die-cut finished pieces.
Besides creating designs digitally, just about everything else for White's Typebee projects is done manually. She mixes ink by hand. She feeds individual sheets of paper into the press by hand. She maintains and oils the presses by hand.
"For me, it's more the process that goes into it," White says of it all. "You have to think from the end of the final product and come back to the beginning."
As she's focused on honing the art of old-craft style printing — a trend that's risen along with other handcrafted, artisan movements in the past decade — White has worked to master both the creative and technical aspects of the trade, one that's close to being lost to history as the printing industry evolved.
"There is a big generational gap in the older pressmen and those who've fallen in love with the process" more recently, she says. "Not just in knowledge of [the letterpressing process] but mechanical things. When something would break, we would call a guy to come fix it and he's like 75 years old, so I realized I had to learn to fix these things, too."
While gleaning as much mechanical know-how as she can from these experienced printers and mechanics, White also describes herself as a "pro jerry rigger." Many a time, she's had to implement makeshift fixes, like duct-taping a belt wheel, on her presses to keep them running.
"My favorite part about the whole letterpress thing is that I feel like I understand the press and I know how it works," she says. "I can't do what the machine can do, but it can't operate without me. ... There is this really neat relationship between the printer and the machine. We're both giving to get this certain output."♦
Follow Breanna White on Instagram @Typebee, and on Facebook; facebook.com/typebee.letterpressprintshop